碳化硅(SiC)陶瓷具有优异的高强度、耐高温、耐腐蚀性能和良好的导热性能,成为严苛工况下热交换器的理想材料。在核能、太阳能、煤电等关键领域,SiC陶瓷发挥着不可或缺的作用,为推动节能减排、助力实现“双碳”目标提供了重要技术支撑。当前,开发具有更高热导率的SiC陶瓷材料,已成为实现高效节能的紧迫需求。理论上,SiC单晶的热导率可达490 W/mK,但实际上,受晶格缺陷、杂质元素以及晶界残留相的影响,SiC陶瓷的热导率显著降低,通常介于30-270 W/mK之间。尤其是晶格氧杂质,因其引发的强烈声子散射效应,被公认为制约SiC陶瓷热导率提升的关键因素。
针对上述挑战,中国科学院宁波材料技术与工程研究所浙江省全省数据驱动高安全能源材料及应用重点实验室自2023年起,锚定高热导率SiC陶瓷的微观结构设计与制备技术领域,开展系统性攻关研究,在该方向上取得了一系列具有重要价值的创新成果:
1. 诱导β→α相变优化晶界结构
研究团队提出以β-SiC为原料,结合Y2O3-MgO复合添加剂,利用放电等离子烧结技术,成功实现了对SiC陶瓷的β→α相变调控与微观结构优化。当烧结温度从1850 ℃升至2050 ℃时,SiC的β→α相变趋于完成,晶粒尺寸显著增大(中位粒径从0.53 μm增至2.41 μm),晶格氧含量由0.34 wt%降至0.08 wt%。β/α异相晶界的消除大幅减少声子散射,较传统α-SiC原料制备的陶瓷提升61.9%,使热导率从126 W/mK跃升至204 W/mK。该成果揭示了相变驱动晶粒生长与晶格氧杂质排出的关键机制,为制备高热导率SiC陶瓷提供了新思路。

图1 在不同烧结温度条件下,分别以α-SiC和β-SiC作为原料所制备的SiC陶瓷微观结构SEM图片
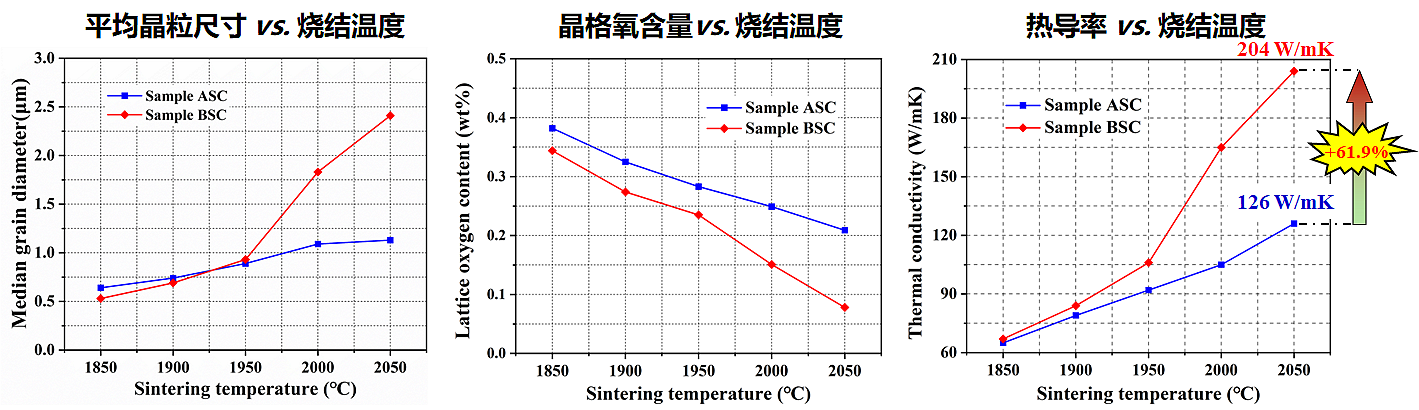
图2 SiC陶瓷晶粒尺寸、晶格氧含量与热导率随烧结温度的变化规律
2. 稀土阳离子场强调控液相特性
团队进一步探究稀土氧化物(RE2O3)与MgO复合添加剂对晶界液相性质的调控规律。研究发现,稀土阳离子(RE3+)半径减小可增强其场强(z/r2),从而优化液相粘度与热稳定性。以Yb2O3-MgO为例,得益于Yb3+适中的阳离子场强,当烧结温度2050 ℃时,该体系不仅有效限制了Yb-Si-Mg-O液相挥发,还显著促进了β→α相变进程与晶粒的选择性生长。最终获得最大晶粒尺寸(8.51 μm)、最低晶格氧含量(0.04 wt%)及无β/α异相晶界的理想结构,热导率高达229 W/mK,刷新了同类添加剂体系的性能纪录。
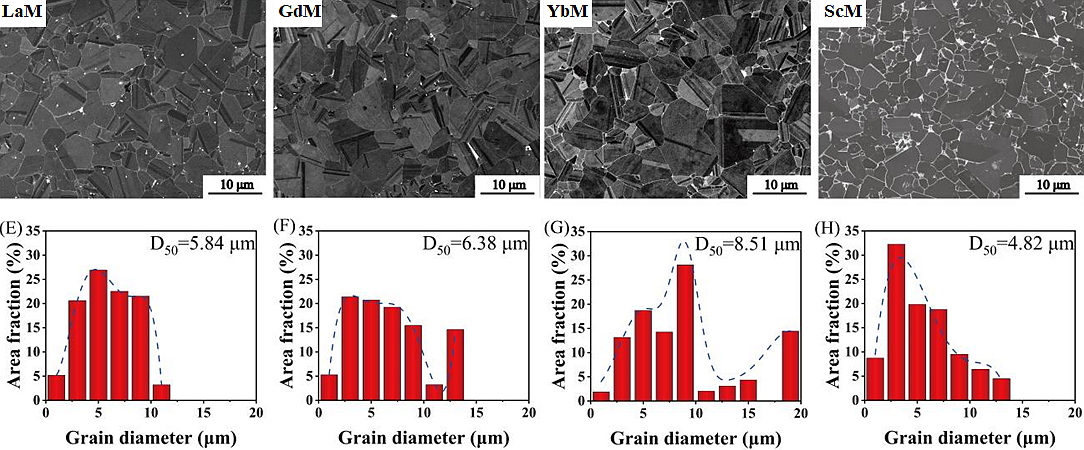
图3 不同稀土氧化物(RE2O3)与MgO复合添加剂制备的SiC陶瓷,微观结构与晶粒尺寸分布统计对比
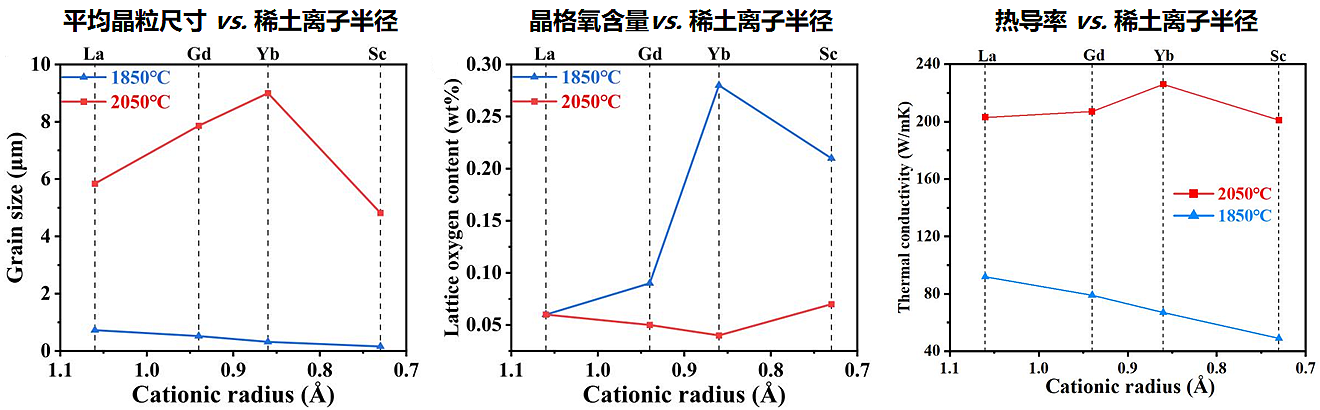
图4 SiC陶瓷的晶粒尺寸、晶格氧含量与热导率随稀土助剂阳离子半径的变化规律
3. 系统性综述提出高热导率SiC陶瓷设计范式
基于上述系列研究成果,研究团队撰写并发表了综述论文“Research progress on high-thermal-conductivity silicon carbide ceramics”,系统梳理了高热导率SiC陶瓷领域的研究脉络与前沿动态,并凝练提出两大核心优化策略:
其一,聚焦微观结构调控,通过降低晶格氧杂质含量、促进晶粒尺寸增长、减少非晶态晶界相占比,可实现热导率的显著提升;
其二,强调原料与工艺协同优化,选用高纯度β-SiC粉体,搭配无铝烧结助剂体系(如Y2O3-Sc2O3),并结合高温烧结工艺(温度>2050 ℃)与适当延长保温时间,是突破热导率瓶颈的关键路径。
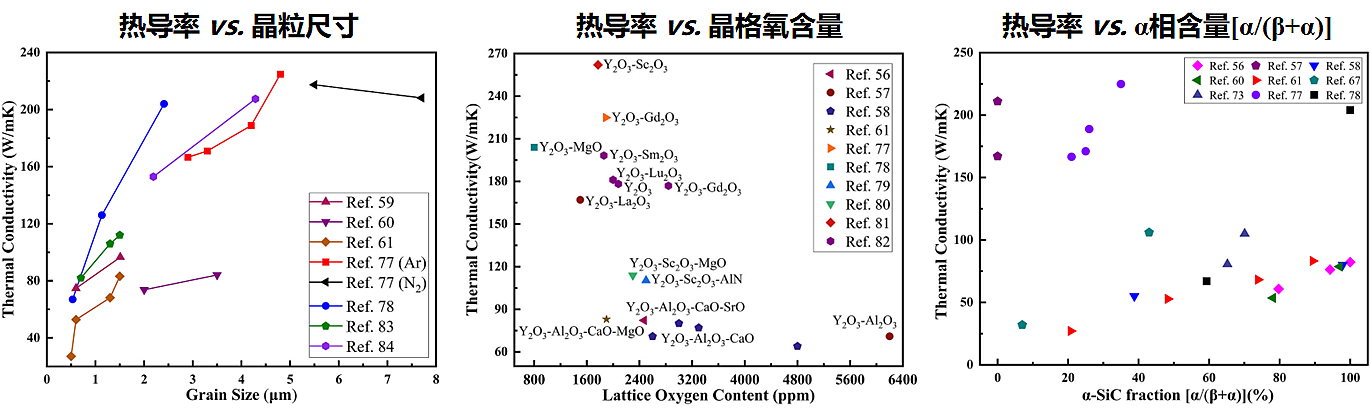
图5 晶粒尺寸、晶格氧含量与α相含量对SiC陶瓷热导率的影响规律
上述成果分别发表于陶瓷材料领域知名期刊 Journal of the European Ceramic Society (原文链接: https://doi.org/10.1016/j.jeurceramsoc.2023.07.036), Journal of the American Ceramic Society (原文链接: https://doi.org/10.1111/jace.20626), Ceramics International (原文链接: https://doi.org/10.1016/j.ceramint.2024.11.408)。本系列研究工作获得国家自然科学基金(52302077),宁波市“科技创新2025”重大专项(2022Z084),宁波市“科创甬江2035”重点研发计划项目(2025Z070)的支持。
实验室将持续深耕硅基特种陶瓷材料研究,推动科研成果落地转化,为保障我国能源供给安全、实现“双碳”目标贡献科技力量。
|