碳化硅(SiC)陶瓷凭借其优异的耐高温氧化、耐腐蚀、耐辐照、高硬度、高导热等性能在航天航空、国防军工、交通、机械、化工等领域有着重要的应用价值与潜力。上世纪70年代日本科学家Yajima首次提出采用先驱体聚碳硅烷制备SiC陶瓷。由于先驱体转化法具有可通过对有机先驱体进行结构设计来调控SiC陶瓷的组分与功能、可利用现有的高分子加工技术获得不同形态的SiC陶瓷材料(包括纤维、涂层、多孔结构等)、可采用先驱体浸渍-裂解工艺(PIP)制备纤维增韧的SiC陶瓷基复合材料等诸多优点,已成为继传统的粉末成型工艺后制备SiC陶瓷的重要方法之一。
聚碳硅烷是主链由硅和碳原子组成,硅和碳原子上连接有氢或其它有机基团的线形或支化结构的高分子。 由于聚碳硅烷结构中含有富碳的基团,所以由其转化的SiC陶瓷富碳。这些富余碳在微观形貌上是分布在SiC晶粒周围并独立存在,不会通过sp3杂化与Si或其它原子进行化学键连接,所以又被称为“自由碳”,“游离碳”或“sp2-杂化碳”。自由碳的存在对聚碳硅烷转化的SiC及其复合材料的结晶性、耐高温氧化性、机械性能、导电性能、电磁性能等都有着至关重要的影响。因此,调控聚碳硅烷转化的SiC陶瓷中的自由碳含量具有显著的意义。目前的调控方法主要包括聚碳硅烷结构调控和气相热解法。结构调控中,减少聚碳硅烷中的不饱和基团可以进一步降低残余碳含量,但不利因素是会导致陶瓷产率降低。气相裂解法是指在聚碳硅烷转化SiC陶瓷过程中,通过气相反应除自由碳,如在由聚碳硅烷制备SiC纤维过程中,通入氢气进行脱碳处理,得近化学计量比SiC纤维。但气相裂解法受限于气体的扩散和渗入,主要适用于纤维、微粉等细微材料。
先进核能材料实验室长期从事聚碳硅烷合成、交联成型及转化SiC陶瓷与SiC陶瓷基复合材料。在自由碳调控方面,采用聚碳硅烷与纳米Si复合,将自由碳转化为SiC(图1)。由于限制SiC晶粒生长的石墨层状结构的减少或消失,SiC晶粒尺寸增大,为固态聚碳硅烷(PCS)转化的SiC的晶粒尺寸随着纳米Si含量的增加而增大(图2);相应地,也能提高转化的SiC的热导率,比如采用纯液态聚碳硅烷制备SiCf/SiC复合材料,经1600 °C热解后室温热导率为3.3 W/m·K,而添加理论量纳米Si后,室温热导率提升至30.5 W/m·K,达到化学气相渗透(CVI)工艺的复合材料热导率;而且,纳米Si还能捕捉聚碳硅烷裂解的气体小分子,从而提高陶瓷产率,比如纯液态聚碳硅烷热解至1600 °C,陶瓷产率为72.0 wt%,添加理论量纳米Si后,陶瓷产率提高至81.8wt%。该方法适用于不同结构和自由碳含量的聚碳硅烷,也适合大体积的块体材料或复合材料。此外,也通过向聚碳硅烷中引入镍系化合物,可催化部分自由碳转化为碳纳米管(图3),有利于提高SiC陶瓷的电导率和热导率。
以上相关工作发表在国际陶瓷领域学术期刊上(Journal of The European Ceramic Society, 2024, 44(13):7482–7489;Ceramics International, 2024, 50(13): 22771–22782;Silicon, 2025, https://doi.org/10.1007/s12633-025-03245-3),并获得浙江省重点研发计划(Grant No. 2022C01236)、先进能源科学与技术广东省实验室(Grant No. HND20TDTHGC00)、宁波市“3315”创新团队计划(Grant No. 2018A-03-A)等项目的支持。
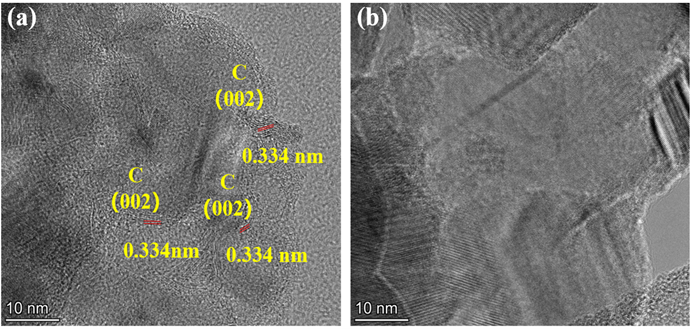
图1. (a) 聚碳硅烷转化SiC; (b) 聚碳硅烷+纳米Si转化SiC
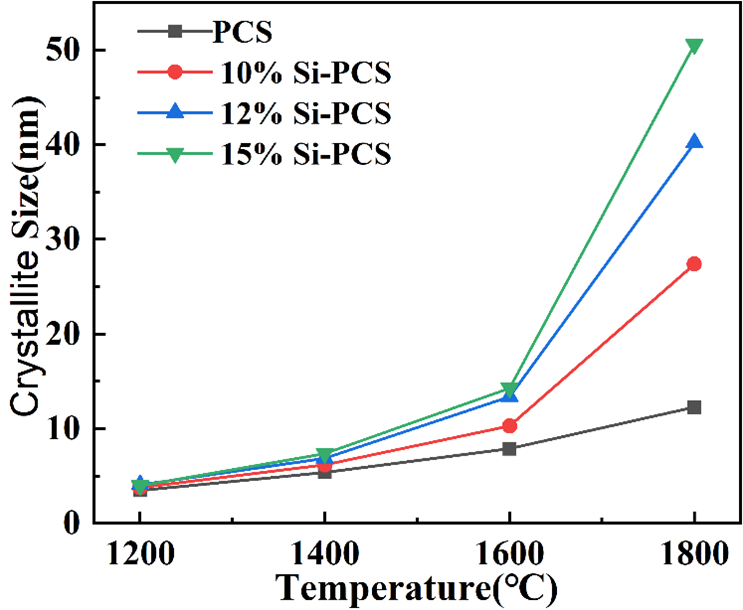
图2. 固态聚碳硅烷转化SiC的晶粒尺寸随纳米Si含量变化
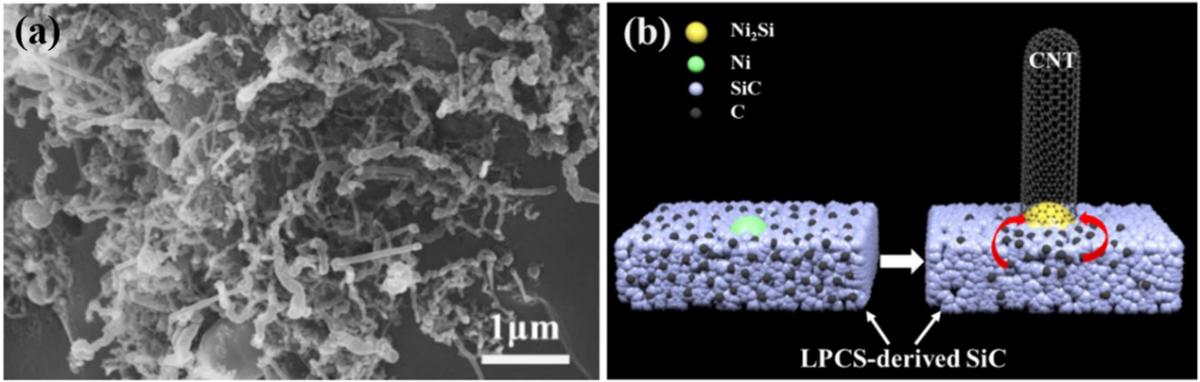
图3. (a) 镍系化合物催化聚碳硅烷中自由碳转化碳纳米管; (b) 碳纳米管形成机理
|